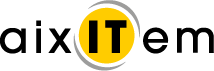
Unsere Referenzen
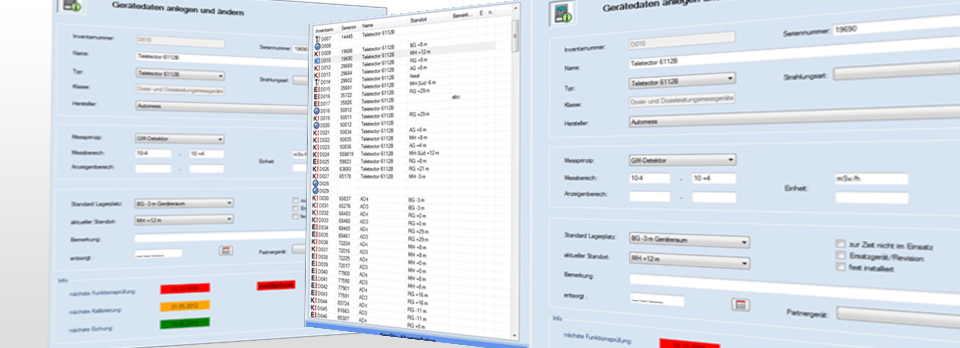
Ausgangslage
In einem Schweizer Kernkraftwerk sind radioaktive Strahlenquellen und verschiedene Typen von Messgeräten des Strahlenschutzes zur Kontrolle von Strahlendosen und Dosisleistungen, Kontaminationen und zur Überprüfung der Luft vorhanden. Diese unterliegen umfangreichen behördlichen Vorgaben und Auflagen des Eidgenössischen Nuklearsicherheitsinspektorats (ENSI), deren Erfüllung regelmäßig nachgewiesen werden muss und die bisher sehr zeitaufwändig war.
Die Geräte befinden sich an verschiedenen Standorten und müssen regelmäßig kontrolliert, kalibriert und geeicht werden. Die Prüfvorschriften greifen auf Strahlenquellen zu, deren Aktivität sich ständig ändert und die ihrerseits ebenfalls regelmäßig überwacht werden müssen. Flüssige Quellen können im Bereich der Chemie beliebig geteilt und gemischt werden. Neben der Stammdatenverwaltung sollen die oben erwähnten Auflagen bezüglich lückenloser Dokumentation unterstützt und gewährleistet werden.
Herausforderung
Der Algorithmus für die Kalibrierung von Messgeräten mit hoch radioaktiven Quellen auf einer speziellen Bestrahlungsanlage muss den Anforderungen des Paul-Scherer-Instituts genügen und wurde von diesem geprüft und zertifiziert. Die ENSI-Berichterstattung soll auf Knopfdruck geschehen. Das Programm wurde zunächst in einer Basisfassung erstellt und über viele Jahre systematisch erweitert und neuen Anforderungen angepasst.
Technik
Das System wurde mit Microsoft Visual Studio, C# und einer SQL-Datenbank für Windows7 umgesetzt.
Welche Strahlenquellen sind im Bestand, welche neu beschafft, welche entsorgt worden?
Das System liefert die gewünschten ENSI-Listen auf Knopfdruck.
Wann muss mein Messgerät überprüft, kalibriert oder geeicht werden bzw. meine Strahlenquelle geprüft werden?
Das System erlaubt die Terminüberwachung von 3 Terminen pro Gerät (Funktionsprüfung, Kalibrierung, Eichung) und 2 Terminen pro Strahlenquelle (Dichtigkeitsprüfung, Standortprüfung). Es können Fälligkeitslisten nach verschiedenen Filtern erstellt werden.
Wann wurde das Gerät an welchem Standort genutzt?
Das System gibt jederzeit darüber Auskunft, an welchen Standorten sich das Gerät jemals befunden hat bzw. aktuell befindet.
Wann war das Gerät defekt und wer hat es repariert?
Das System verwaltet gemeldete Fehler und die Art der Reparatur. Reparatur- oder Wartungsprotokolle werden erstellt und können durch gescannte Dokumente ergänzt und jederzeit wieder eingesehen werden.
Wie ist die Historie meiner Strahlenquelle?
Mit flüssigen Strahlenquellen wird gearbeitet. Sie können verdünnt, geteilt und/oder gemischt werden. Das System berechnet automatisch die neuen Aktivitäten und verwaltet die Historie der Quellen, so dass jederzeit nachgesehen werden kann, wann welche Quelle wie verändert wurde.
Welche Strahlenquellen haben welche Aktivitäten?
Das System berechnet in den Prüfvorschriften zur Funktionsprüfung und Kalibrierung die Vorgabewerte für den zu erwartenden Messwert anhand der tagesaktuellen Aktivität der verwendeten Strahlenquelle auf der Basis eines Referenzwertes an einem bestimmten Datum und der Halbwertzeit.
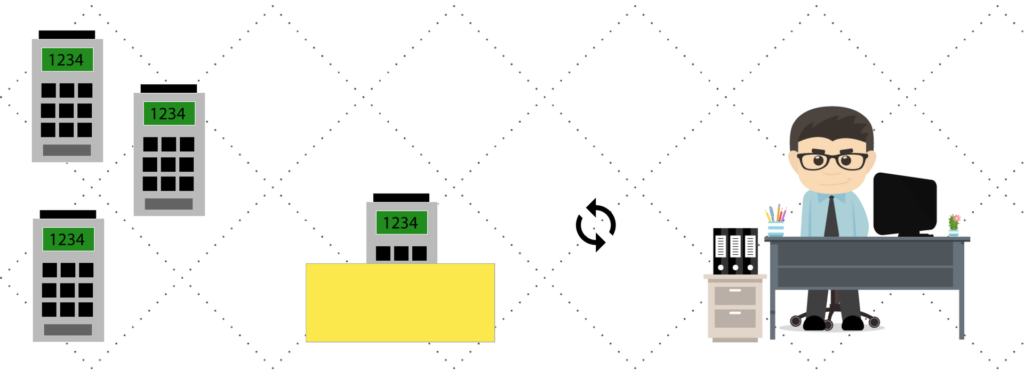
2022
Ausgangslage
Unser Kunde betreibt bereits seit mehreren Jahren ein Gerät zur Kalibrierung von Messgeräten. Die Kalibrierungsdaten wurden bisher über eine R232-Schnittstelle mit einem Drucker auf Papier gebracht und von einem Mitarbeiter wiederum per Hand in eine aixITem Software zur Geräteverwaltung übertragen.
Herausforderung
Das Ziel war es, das Kalibrierungsgerät mit der Geräteverwaltung zu verbinden und somit eine direkte Kommunikation ohne den Umweg über den Drucker und einen Mitarbeiter zu ermöglichen.
Zunächst wurden die involvierten Soft- und Hardware-Schnittstellen analysiert. Speziell das Verhalten des Druckers war entscheidend, da dieser aus dem System entfernt und ersetzt werden sollte. Es galt also eine Komponente zu finden, die die Daten für den Drucker in Eingabedaten für die Geräteverwaltung umwandelt.
Lösung
Für eine direkte Kommunikation vom Kalibrierungsgerät zur Geräteverwaltung wurde von aixITem eine Softwarelösung auf einem Raspberry Pi entwickelt. Dieser recht günstige Einplatinencomputer und ein weiterer Hardware-Baustein simulieren den Drucker, speichern die Nutzinformationen aus den Druckdaten, lesen sie aus und geben sie über die Netzwerkschnittstelle an das Geräteverwaltungsprogramm weiter. Somit wurde der Prozess komplett automatisiert.
Welche Vorteile hat die Digitalisierung?
Der Prozess der Digitalisierung von analogen Daten ist allseits bekannt. Hin und wieder finden wir aber Fälle in denen es anders herum läuft. Es werden bereits digitale Daten durch einen Menschen „analogisiert“ (abgelesen, aufgeschrieben, im Gedächtnis behalten), um dann in ein anderes digitales System übertragen zu werden. Dieser Prozess birgt Fehlerquellen und kostet Zeit. In der Regel spricht man in solchen Fällen von einem Medienbruch. Wir sehen darin die Chance zusammen mit unserem Kunden eine Lösung zu entwickeln, die beide digitalen Systeme miteinander verknüpft und somit den Prozess automatisiert.
Die Komponente Raspberry Pi
Die größten Vorteile eines solchen Einplatinencomputers sind die geringen Anschaffungs- und Betriebskosten. Über Wechseldatenträger (SD-Karten) oder Netzwerkschnittstellen lässt sich nahezu jede Software, die einen gewissen Grad der Komplexität nicht überschreitet, unkompliziert anpassen und warten.

Alexander Willkomm
Projektverantwortlicher
Sprechen Sie mich an, ich berate Sie gerne.
Telefon: +49 241 5330633 0
E-Mail: a.willkomm@aixitem.de
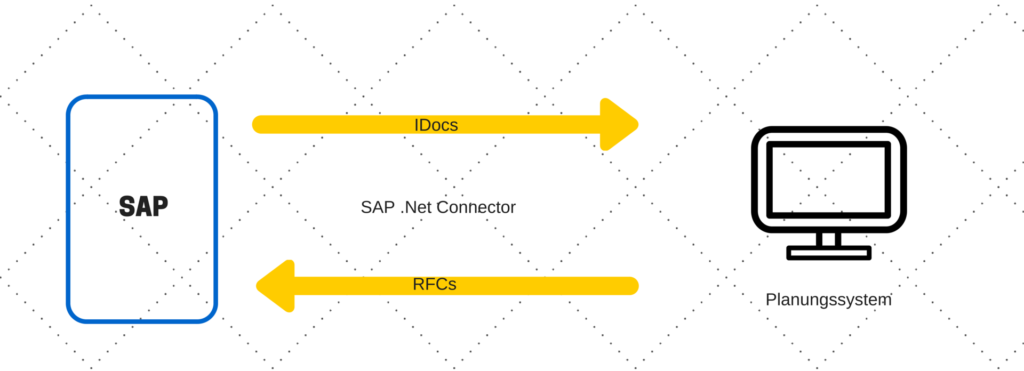
2022
Ausgangslage
Unser Kunde setzt die Planungssoftware FEKOR ein. Die Planungssoftware wird in Produktionsunternehmen für die Fertigungsplanung eingesetzt. Die Planung geschieht in vielen Fällen auf der Basis von Stammdaten und Bewegungsdaten, die in einem ERP-System gepflegt werden. Hierzu bietet das Planungssystem eine Standard-Schnittstelle auf Basis von SQL-Tabellen.
Im konkreten Fall wurden die Daten in einem SAP-System gepflegt. Auf Grund der Konzernrichtlinien war es nicht möglich, die Daten aus dem SAP-System direkt in die SQL-Tabellen des Planungssystems zu übernehmen.
Lösung
Die realisierte Lösung besteht aus zwei permanent laufenden Windows-Diensten. Ein Dienst holt Daten vom SAP-System ab, der andere Dienst überträgt Ergebnisdaten an das SAP-System.
Als Basis für die Kommunikation wurde der SAP .Net-Connector verwendet. Die Übermittlung von Daten aus dem SAP-System geschieht mittels IDocs. In der umgekehrten Richtung werden Remote-Function-Calls (RFCs) verwendet.
Vom SAP werden Daten zu den Artikelstammdaten, zu den Kundenaufträgen (Bedarfen) und zu den Lagerbeständen übertragen.
Von Fekor zu SAP werden RFCs gerufen, welche Fertigungsaufträge in SAP anlegen und die Daten zu den angelegten Aufträgen an neue Planungsergebnisse anpassen. Außerdem werden Warenbewegungen innerhalb der Produktion an SAP gemeldet.
Nutzen
Durch die Schaffung einer passenden Schnittstelle konnte die erneute Erfassung der im ERP-System bereits vorhandenen Daten vermieden werden. Beide Systeme verwenden zukünftig für die kaufmännische Betrachtung und die Produktionsplanung dieselben Stammdaten.

Alexander Willkomm
Projektverantwortlicher
Sprechen Sie mich an, ich berate Sie gerne.
Telefon: +49 241 5330633 0
E-Mail: a.willkomm@aixitem.de
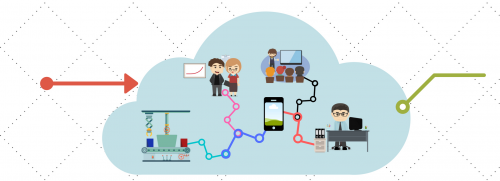
Kennen Sie das? Ihre Eingabemasken und digitalen Formulare sind überfüllt mit Feldern und Informationen und Sie verlieren schnell den Überblick bei der Bedienung Ihrer IT-Systeme.
Eingabedialoge und Masken in Standardsystemen sind oftmals kompliziert zu bedienen. Viele Auswahl- und Eingabemöglichkeiten machen die Benutzung unnötig komplex. Lösung schafft individuelle Dialogentwicklung von aixITem, damit sich Ihre Mitarbeiter auf das Wesentliche konzentrieren können.
Unsere Systeme werden vollständig in Ihre IT-Welt integriert. Diese Integration wird über Schnittstellen oder Anpassung Ihrer Standardsoftware erreicht.
Nachfolgend haben wir einige Beispiele für Sie zusammengestellt:
Lösungsszenarien
Es gibt viele Möglichkeiten, die Datenerfassung auf Ihre Bedürfnisse anzupassen. Nachfolgend einige Beispiele:
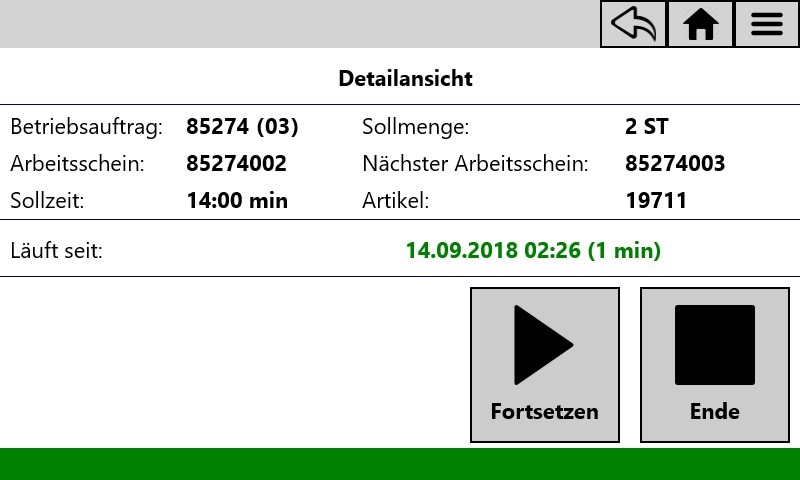
Betriebsdatenerfassung: Reduktion auf das Wesentliche
Bei der Betriebsdatenerfassung im Produktionsumfeld ist Schnelligkeit besonders gefragt. Eingabemasken müssen daher auf das Wesentliche reduziert werden, damit Benutzer nicht unnötig mit bürokratischen IT-Eingaben überlastet werden. Wir analysieren individuell Ihre Anforderungen und entwickeln gemeinsam mit Ihnen eine passende Lösung.
- Viele Szenarien (zum Beispiel Start- / Stop- / Unterbrechungsmeldungen, Mengenbuchung, …) im Standard verfügbar
- Angepasst auf Ihre Prozessanforderungen
- Gute Übersicht
- Voll Integriert in Ihr IT-System (z.B. ERP, PPS, MES,…)
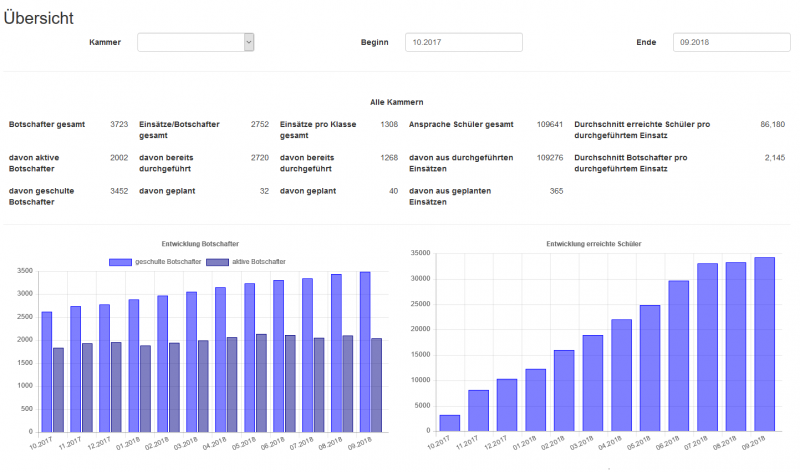
Datenauswertung: Visualisierung
Bilder sagen mehr als 1000 Worte. Bei effizienten und bedienerfreundlichen Dialogoberflächen spielt die Datenvisualisierung eine große Rolle. Wir schaffen mit individuellen Auswertungsmasken die Übersicht, die Sie für Ihr Szenario brauchen.
- Darstellung Ihrer Daten auf Grundlage einer individuellen Analyse
- Dashboards und Cockpits für eine schnelle Entscheidungsfindung
- Flexibel anpassbar als Webseite oder .Net Anwendung
- Vollständig integrierbar in Ihre IT-Landschaft
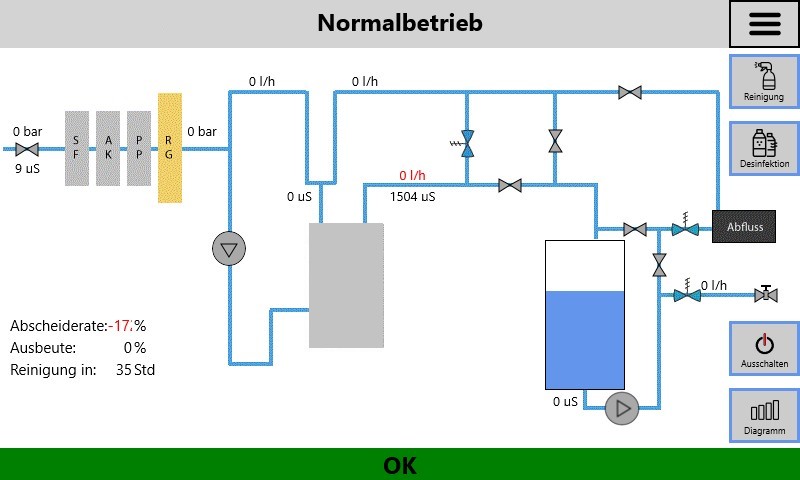
Angepasst: So individuell wie Sie
Wir passen unsere Dialog- und Eingabemasken an Ihre Anforderungen an, so dass Sie Ihre gewohnten Begrifflichkeiten sowie die gewünschten Darstellungsvarianten und Abläufe erkennen können. Somit bildet das IT-System die reale Umgebung ab. Gemeinsam mit Ihnen entwerfen wir alternative Szenarien, die Ihre Prozesse vereinfachen.
- Anpassung an Ihre Prozessen
- Überprüfung der Prozesse, ob durch Digitalisierung neue Potentiale genutzt werden können.
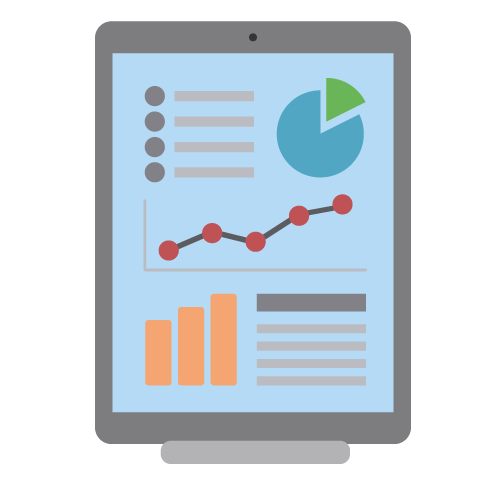
Flexibel: Auf unterschiedlichen Geräten
Die Art der Eingabe ist wichtig. Passt zu Ihnen eine Erfassung über Touch-Display? Oder ist eine Eingabe mit haptischen Tasten für Sie die beste Wahl? Lassen sich Daten automatisch erfassen, ganz ohne Benutzereingabe? Dank unserer langjährigen Erfahrung haben wir die passende Lösung für unterschiedliche Anforderungen.
- Eingabe über verschiedene Systeme (Touch-Display, haptische Tastenblöcke, …)
- Anbindung externer Sensorik zur automatischen Erfassung
- Vollständig integriert in Ihre IT-Umgebung
Ihre individuelle Lösung auf Grundlage von aixITem Basis-Software
Wir schaffen unsere Lösungen auf Grundlage unserer Basis-Module, die wir mit einer Erfahrung aus über 20 Jahren Softwareentwicklung aufgebaut haben. Somit bieten wir Individualität zu einem fairen Preis. Sprechen Sie uns gerne an. Heben Sie Ihre Dialogsysteme auf das nächste Level!
Ein erstes Beratungsgespräch
Sie wollen mehr über die Möglichkeiten von aixITem IoT erfahren? Vereinbaren Sie einen Termin mit uns!
- Lernen Sie uns unverbindlich kennen
- Beispiellösungen
- Analyse des Digitalisierungspotentials

Ausgangslage
In Prozessen mit hohem Automatisierungsgrad werden unvorhergesehene Einflussfaktoren auf das Produktionsergebnis häufig erst viel zu spät erkannt. Es ist deshalb dringend erforderlich unerwartete Fehlerhäufungen und Fehlertendenzen frühzeitig zu erkennen.
Unser Kunde stellt in einem zweistufigen Prozess Kunststoffstreuscheiben für Fahrzeugscheinwerfer her. Die Streuscheiben werden paarweise gespritzt und anschließend lackiert. Alle produzierten Streuscheiben werden in einer manuellen optischen Kontrolle auf Fehler geprüft. Bei der Kontrolle werden Handschuhe getragen. Der festgestellte Ausschuss wurde handschriftlich protokolliert.
Herausforderung
Das gesuchte System sollte die Erfassung des Ausschusses in der Produktionshalle in möglichst einfacher Form ermöglichen. Hierbei sollte insbesondere berücksichtigt werden, dass die Bedienung nicht mit den Fingern erfolgen soll, damit keine Übertragung von Schmutzteilchen auf die Streuscheiben erfolgt.
Für die Produktionsverantwortlichen soll das System jederzeit einen Überblick über die aktuelle Ausschusssituation in der Produktion geben. Der Einrichter soll ein Analyseinstrument zur Erkennung unerwarteter Fehlerhäufungen erhalten. Der Erfolg einer Abstellmaßnahme soll schnell erkennbar sein.
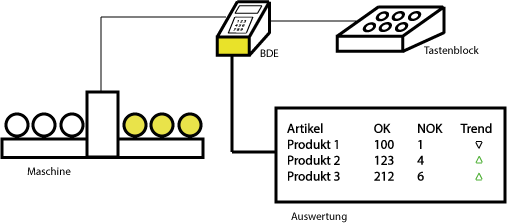
Lösungsweg
Die installierte Lösung besteht aus einer Kombination von Hardware- und Softwarekomponenten. Ein BDE-Terminal erhält die Informationen zu den produzierten Teilen direkt von den Maschinen. Zwei spezielle Tastenblöcke (rechte und linke Seite) erlauben die Erfassung der Ausschussgründe. Die Taster auf den Blöcken sind so angeordnet, dass sie eine Bedienung mit dem Handrücken erlauben. Somit wird eine Verschmutzung der Handschuhe im Bereich der Finger ausgeschlossen.
Die vom BDE (Betriebsdatenerfassung) – Terminal gesammelten Daten werden online in einem Leitstand visualisiert. Die farblich dargestellten Warnschwellen und Fehlerschranken können pro Artikel individuell definiert werden. Sie signalisieren dem Entscheider in der Produktion frühzeitig wenn kritische Situationen entstehen. Über eine zusätzliche Berechnung des Fehlergradienten ist eine Visualisierung der Tendenz möglich, die besagt, ob die Fehlerhäufigkeit aktuell zu- oder abnimmt.
Für spätere Auswertungen werden die Produktionsdaten in einer Datenbank gespeichert. Hierzu werden die Informationen pro Schicht und Tag verdichtet.
Kurzfristiger Nutzen für den Kunden
Mit Einführung des Systems konnte die handschriftliche Aufschreibung des Ausschusses und die manuelle Übertragung in Excel-Tabellen eingestellt werden. Alle Daten können direkt aus der Datenbank ausgewertet werden.
Das Ausschusserfassungssystem gibt zu jedem Zeitpunkt einen aussagekräftigen Überblick zum Zustand der Produktion. Die Einrichter werden sofort informiert, wenn eine nicht erwartete Fehlersituation eintritt. Sie können Fehlerursachen sofort beseitigen, indem sie z.B. Anlagenteile nachjustieren oder reinigen. Die Tendenzanzeige gibt eine sofortige Aussage darüber, ob die ergriffenen Maßnahmen Auswirkungen auf das Produktionsergebnis haben.
Langfristiger Nutzen
Durch die ständige Beobachtung der Produktion und die sofortige Behebung von Fehlerursachen konnten die Ausschussquoten deutlich reduziert werden. Da die Fehler zeitnah erkannt werden wurde die Fehleranalyse deutlich vereinfacht.
Bei der Optimierung der Anlagen konnten gezielt die Anlagenteile verbessert werden, die häufig als Ursache für Ausschuss identifiziert werden.
Das System wurde in einer weiteren Ausbaustufe um die Überwachung der Taktzeiten der Maschinen erweitert. Dies wird insbesondere im Bereich Spritzgießen eingesetzt um technische Probleme der Anlagen frühzeitig zu erkennen.
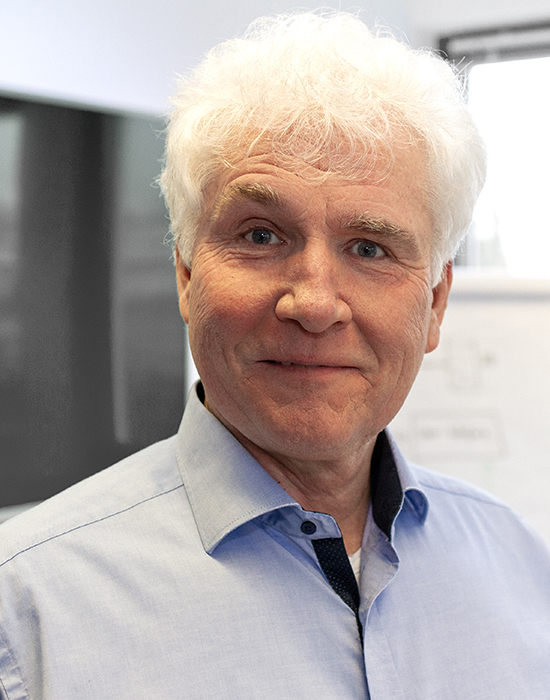
Harry Studer
Projektverantwortlicher
Sprechen Sie mich an, ich berate Sie gerne.
Telefon: +49 241 5330633 0
E-Mail: h.studer@aixitem.de